
I'm making 3d-models for fursuits and hand puppets for about a year now and I print them on my FlashForge Creator 3D-printer. I have made 3d-models for head-bases, claws, noses, eyelids, footpads and teeth. I've tried several materials and settings to get the best printing results. It was a long learning-process. It's time to share my experiences.
Why 3D-printing:
Initially, I'll have to say that 3D-printing for the construction of a single fursuit head is not faster, cheaper or simpler than any other construction method. If you want to make many items, it may be worth the costs. A big advantage of 3D-printing is that you can recreate a 3d-printd part again and again - this makes it much easier to try new things (without having the worry about breaking something that cannot be replaced) and it makes repairs very simple. I bought the 3d-printer to have more spare time - the printer can do the work while I do something else - so far that worked very well.
How to create a 3d-model:
I start to model a head-base as NURBS model (https://en.wikipedia.org/wiki/Non-uniform_rational_B-spline). Unlike polygon-models, it is much easier to change the shape of a NURBS-model without having to adjust a lot of points. I could do the same with a polygon-model, but this saves me a lot of time - it requires software that can handle it. In the first step, only the outer surface is defined.
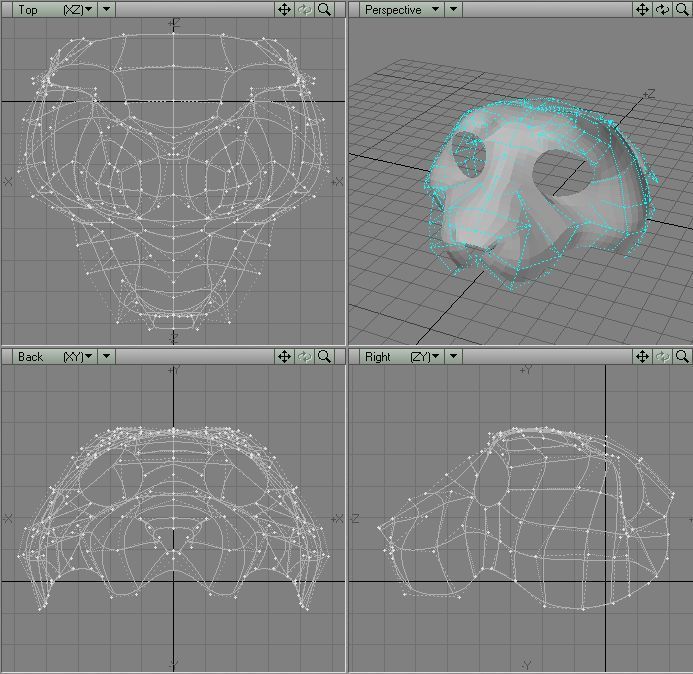
When I'm satisfied with the surface the model is converted into a polygon model.
The resulting polygon-mesh is then made to a model with volume - a wall thickness of 2,5-4mm works for me (3mm is usually ideal).
All polygons should now consist of three points and the surface should point outward. Only 2 polygons should meet at each edge.
This model is then exported in OBJ-format
In NetFabb I check whether the model has flaws - and repair them if necessary.
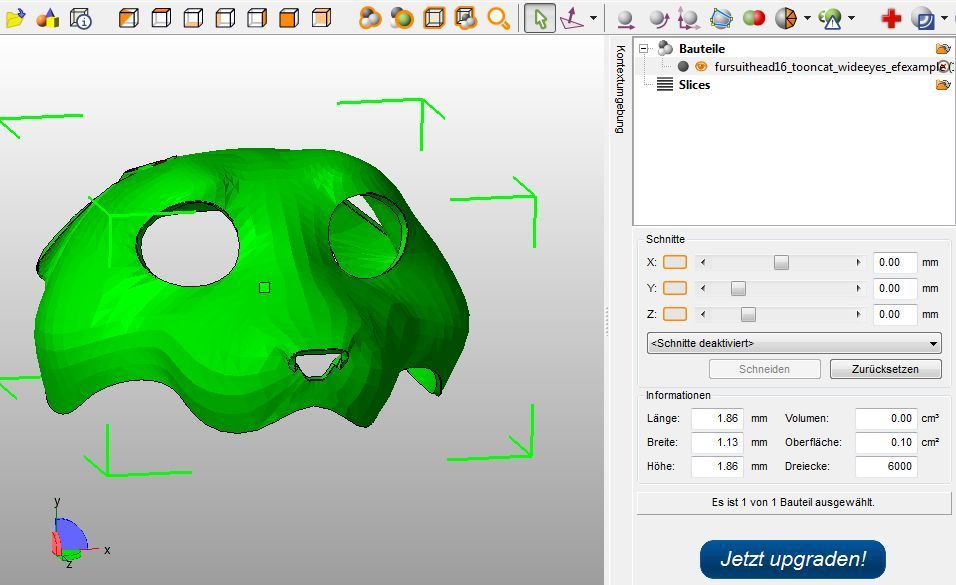
The model is then cut to have a surface that can stand on the print bed.

The models are aligned on the print bed in the 3D-printing software.
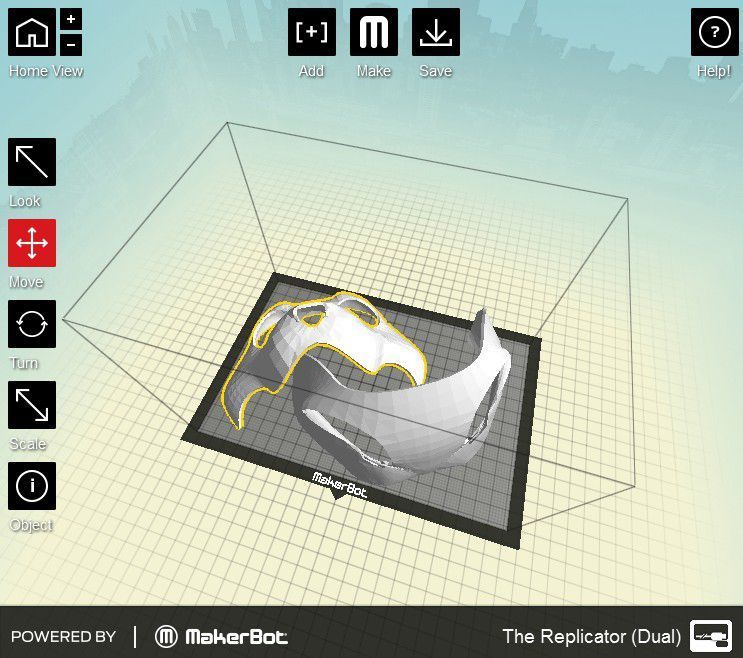
For printing, the model is divided into layers that are printed from the bottom up.
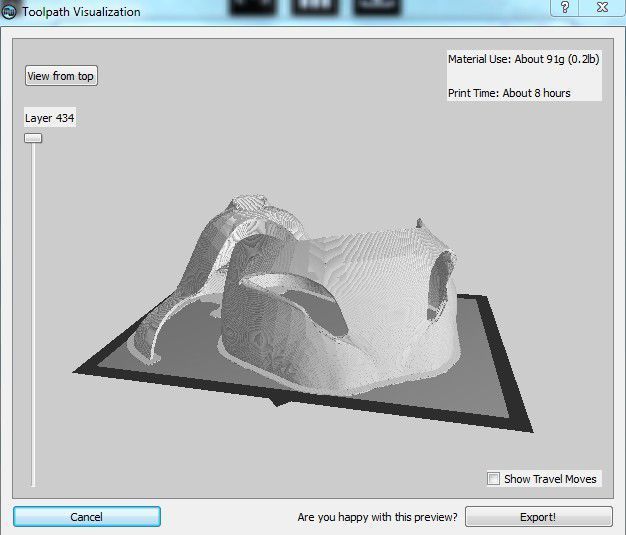
I mostly use an old version of LightWave Modeler to model - because I know the software and already have it. A cheaper alternative to the LighWave Modeler is
Metasequoia http://metaseq.net/en/index.html
What software is used does not matter much - as long as it can produce a polygon-model in OBJ- or STL-format.
Free tools to create 3d-models:
Autodesk 123D (123D design, Meshmixer Thinkercad, ...): http://www.123dapp.com/
Blender: http://www.blender.org/
Sculptris: http://pixologic.com/sculptris/
OpenSCAD: http://www.openscad.org/
Netfabb Basic: http://www.netfabb.com/
Materials for FDM / FFF printers:
What materials can be used for 3D printing depends primarily on the 3d printer. Most important is the printing temperature and the stiffness of the filament. Some printers are built for PLA only and are not able to print at higher temperatures. Some printer cannot use flexible filament.
PLA
Prints at low temperature (200-230 °C)
Based on corn starch
Can be easily printed compared to ABS filament.
May break when it is printed too thin (you should have a minimum wall thickness of 2mm everywhere)
Nearly odorless during processing (I think it smells little like popcorn)
Does not warp much
Can be printed without heated plate - the best printing results are achieved when the extruded filament is cooled immediately after exiting the extruder
Can be sanded, drilled, painted.
Flexible PLA
Prints at low temperature (220-235 ° C)
Similar to rubber
Very flexible and resilient
Does not break
Warps during cooling
Not suitable for higher thinner structures
ABS
High printing temperature as PLA (235-255 ° C)
Stinks
Can be dissolved and glued with acetone.
More flexible than PLA
Warps during cooling (closed printing chamber and heated printing-plate should be used - the heat must remain in the printer)
Bendlay
Highprinting temperature (215-240 ° C - works best at 240 ° C)
Almost transparent
More flexible than PLA, stiffer than ABS
Stinks
Warps a lot while cooling
Nylon
Highprinting temperature (245-255 ° C)
Nearly odorless
Very strong and flexible material
Does not break
Above a 2mm wall thickness it can only be destroyedwith a tool
Warps while cooling (larger objects must be glued to the prind-bed)
Must be stored absolutely dry before processing
Can be dyed
I prefer PLA and Nylon. Nylon for fursuit heads, PLA for noses, eyelids, etc. Nylon is more difficult to process than PLA and requires some preparation. I print both on M3 Scotch-Blue Painter's Tape.
Tips for printing nylon
For Nylon I use a glue-stick on the blue tape and secure the tape with clamps on the print-bed. I print with raft and glue the first layer of the raft to the tape with superglue. The ends of the Nylon-print tend to shrink so much that they pull the tape from the print-bed – I make sure the ends are on the edge of the prind-bed – afte the 10th layer I use a clip to the end of the raft to hold it on the print-bed.

My experiences with different filament:
If the filament gets stuck in the extruder while printing it is caused by the material most of the time. It does not matter how expensive the filament is - many manufacturers provide extremely poor quality, I had
filament that broke during unwinding
extreme variations in the diameter
metal scraps in the material (that clogs the extruder)
oval Material
improperly stored material (nylon, with a lot of moisture)
I can only recommend the dealer to change when problems occur frequently. Currently I buy PLA for 19.95€ per kilo and I am very happy with it.
The FAQ:
Where can I print?
Commercial 3d-printing services:
Shapeways: https://www.shapeways.com/
Sculpteo: http://sculpteo.com/
Rapid Object: http://rapidobject.com/
I.Materialise: http://i.materialise.com/
Hack Spaces, FabLab
Find 3d-printer owners in the vicinity
Which 3D printer is right for me?
That depends on:
What materials do you want to use?
What is the maximum resolution that you need?
How big do you want to print?
How big is your budget?
Do you want to assemble the 3d-printer?
http://3dprint.com/34667/flowchart-3d-printer/
Compare the printers:
Where can you find 3d-models for printing?
Search: http://www.yeggi.com/
Is PLA stable enough for a fursuit head?
A fursuit-head-base with 3mm wall thickness is very tough - similar to a resin head. I've stood on a head with 4mm wall thickness - 70kg did not break it. One head fell on the floor (from approx 1.70m height on hard stone floor) – it has not taken any damage.
Why Nylon for a fursuit head?
I wanted a fursuit head that I could check in with normal luggage.
It should also be flexible and last a long time. Nylon meets these requirements.

How does 3d-printing work?
Most customer 3d-printers work by squeezing melted plastic filament through a thin nozzle (Fused Filament Fabrication).
How do I design a model for 3d-printing?
- Make sure the model is seamless (no holes)
- Make sure all polygones have 3 points
- Make sure all polygones point to the outside
- Eliminate non-manifold geometry
- Make sure the model has no thin walls - the smallest feature is double the nozzle width
- 45 degree rule (if you print without support-material overhangs should not exceed 45°)
- For objects with multiple interlocking parts, design in your fit tolerance
- Orient for the best resolution
- Don’t use additional shells on fine featured models, like small text. It will obscure the detail.
- Orient your model to minimize stress on the part by orienting the model so that the print lines are perpendicular to point of the pressure being applied